
Let’s discuss the basics of cutter blade knowledge and offers suggestions for troubleshooting cutting issues.
CUTTER BLADE DESIGN
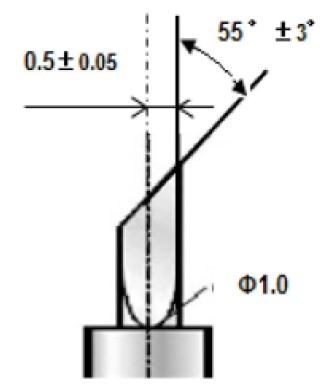
- 0.5 ±0.05 Offset: Distance from the center of the blade to the edge of the blade. The offset determines the
blade’s turning radius and how it compensates for distance while turning corners. Offset is specified by the
blade manufacturer. - 55° Angle: The angle is specified in the measurement of degrees. The blade below is a 55-degree blade.
- Ø1.0 Circumference: Lists the circumference of the blade tip.
BLADE EXTENSION – CUTCONTOUR
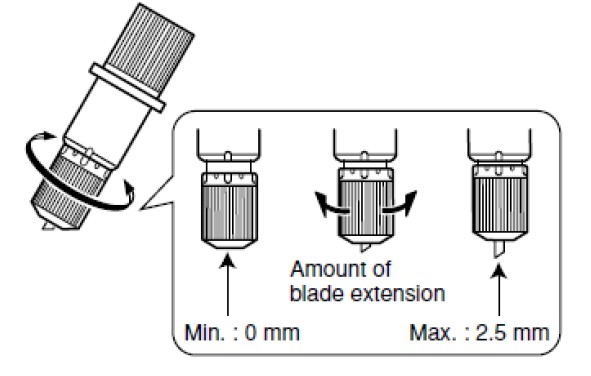
- Blade extension is adjusted by twisting the blade holder’s cap.
- Blade extension should be minimized for substrates. The blade is often extended too far.
- A good strategy to start with is to extend the blade the length of half the thickness of a credit card. Then send a
cut test to determine if more downforce is required and/or if more blade extension is required.
BLADE EXTENSION – PERF CUTCONTOUR
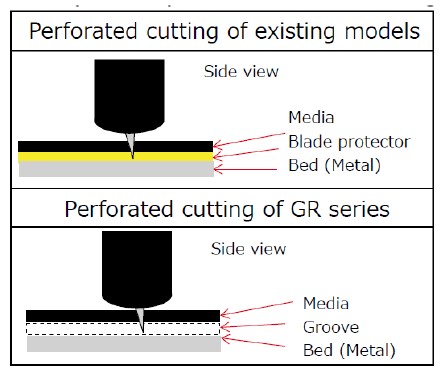
NO GROOVE IN PLATEN
- The blade is extended the same length as CutContour cutting for Roland devices that do not have a designated groove for perforated cutting. The reason is the blade makes contact with the blade protection strip and overextending the blade can severely damage the cutter protection strip.
- This strategy applies to Roland printer/cutters and the CAMM-1 Pro GS-24 and GX-24 models.
GROOVE IN PLATEN
- The blade is extended further for devices with a dedicated groove in the platen for perforated cutting.
- A good strategy to determine how far to extend the blade is to take the material you are going to perfcut and fold it over on itself. Then drag the blade holder over the material. The ideal blade extension length is achieved when the first layer of material is cleanly cut (including through the liner) and the second layer is barely scored. If both layers are cut then the blade is extended too far. If the first layer is not cleanly cut then the blade extension length is too little.
- This strategy applies to the CAMM-1 GR cutter series.
BLADE SETTINGS
The optimal blade settings by application. These are general guidelines only and it is always recommended to send a cut test before sending any jobs.
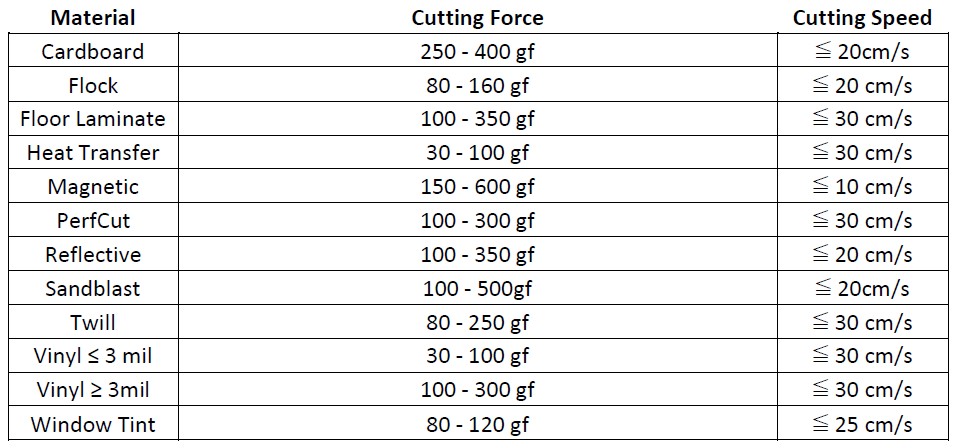
TROUBLESHOOTING
Common cutting issues and possible solutions.
BLADE SKU’S
Pick the best Roland blade for your application. Please note, the list of applications is a general guideline only.
BLADE APPLICATIONS CHART
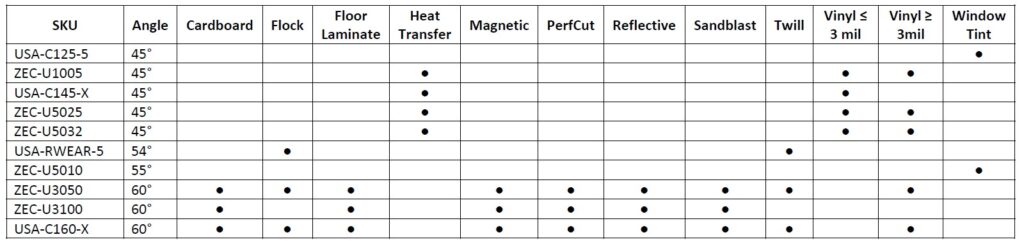
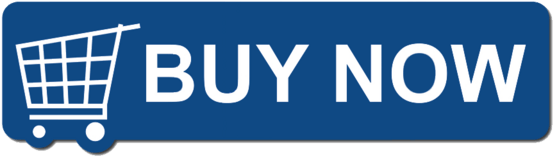